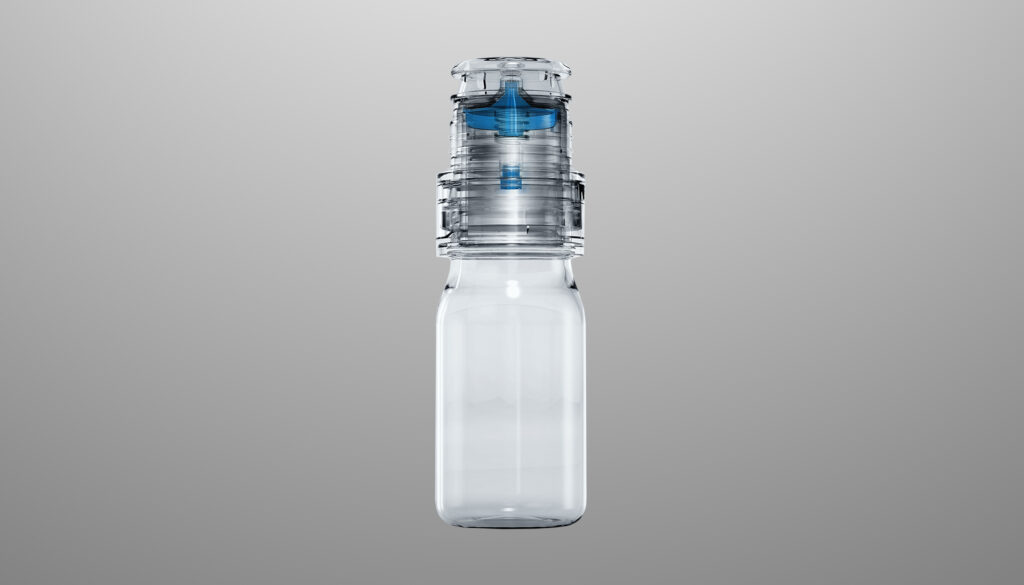
Preservative-free multi-dose spray devices are becoming increasingly popular due to their advantages in patient safety, comfort, and the growing demand for natural or sensitive-skin-friendly products. In the pharmaceutical, cosmetic, and personal care industries, there is a noticeable shift towards formulations that do not rely on preservatives, which are often seen as a source of irritation for sensitive individuals. However, the challenge with multi-dose sprays lies in preventing microbial contamination while ensuring the drug or active ingredient remains stable, effective, and safe throughout multiple uses. Technological advancements in spray device design and formulation have made it possible to overcome these hurdles, enabling the creation of innovative, preservative-free products that are both safe and efficient.
Preservative-Free Multi-Dose Spray: A Growing Demand
A preservative free multi dose spray refers to a drug or treatment spray that can be used multiple times without the need for added preservatives, which are typically included to prevent bacterial growth. In many traditional multi-dose products, preservatives are essential to ensure safety by inhibiting microbial contamination after the container is opened. However, preservatives can cause allergic reactions or irritation for some users, especially in sensitive populations or in products meant for delicate applications like eye drops or nasal sprays. This has led to a growing demand for preservative-free formulations, particularly in products intended for people with allergies, children, or those with compromised immune systems.
To address this need, developers have been working on advanced formulations and packaging technologies that ensure the product remains sterile and effective throughout its multiple uses without the addition of preservatives. These innovations focus on improving the quality and integrity of the formulation, while also ensuring that the product remains safe and effective through the entirety of its shelf life and usage period.
Technological Innovations in Packaging and Device Design
- Airless Pumps and Vacuum-Sealed Containers One of the key innovations driving the development of preservative-free multi-dose sprays is the airless pump and vacuum-sealed packaging. These systems use a special mechanism to prevent the entry of air or external contaminants into the product, which is crucial for maintaining the sterility of the spray over multiple doses. With an airless pump, the product is dispensed from a sealed container without exposing the contents to the outside environment, effectively preventing microbial growth. Vacuum-sealed containers create a similar protective environment, ensuring that no air enters the system, which could lead to oxidation or contamination.
These types of packaging are particularly effective in products like nasal sprays or eye drops, where contamination could significantly impact patient safety. The design prevents the introduction of microbes, providing an added layer of protection without the need for preservatives. - One-Way Valve Technology Another significant development in preservative-free multi-dose sprays is one-way valve technology. This technology ensures that the product is dispensed in a controlled manner and prevents external air or bacteria from entering the container. As the product is sprayed, a one-way valve allows the formulation to exit, but it closes tightly once the dispensing action stops, creating a barrier that maintains the product’s integrity. This is particularly valuable in nasal sprays or other multi-dose products that require precision and repeat use while ensuring that the active ingredient remains free from contamination.
One-way valve systems are also effective at preventing backflow, which could potentially cause microbial contamination. These systems are often paired with specialized materials that help resist bacterial or fungal growth, further ensuring the safety of the product over time. - Microbe-Resistant Materials Advances in microbe-resistant materials used in packaging and delivery devices have further facilitated the development of preservative-free multi-dose sprays. Materials such as antimicrobial plastics or coated components can prevent the growth of bacteria, fungi, or mold within the spray device itself. These materials provide an additional layer of defense against microbial contamination without relying on chemical preservatives. By incorporating these antimicrobial materials, manufacturers can extend the shelf life of preservative-free formulations while ensuring they remain safe for repeated use.
- Sterilization Methods Modern sterilization methods, such as gamma radiation and ethylene oxide treatment, are frequently used in the manufacturing process of preservative-free multi-dose sprays. These techniques ensure that the product and the packaging are completely free of microbial contamination before being sealed and distributed. By sterilizing both the formulation and the container, manufacturers can ensure that the product remains free from harmful microorganisms for the duration of its intended use, thus making the inclusion of preservatives unnecessary.
- Controlled Environment Packaging Another emerging trend is the use of controlled environment packaging, where the product is packaged and stored in an environment that regulates temperature, humidity, and even oxygen levels. This approach helps to maintain the product’s stability and prevents microbial growth. Some packaging systems now include inert gas flushes (like nitrogen) to maintain the product’s stability and further reduce the risk of contamination. By regulating the conditions inside the package, these systems can preserve the integrity of the drug or active ingredient without the need for preservatives.
- Integration of Smart Technology Smart technology is beginning to be integrated into preservative-free multi-dose spray devices. These advanced systems can monitor and control the dosage, spray mechanism, and even track the usage history. Sensors within the device can detect any exposure to harmful environmental factors (such as light or excessive temperature) and alert users if the product’s efficacy is compromised. Such innovations ensure that the product is not only preserved in the absence of preservatives but also used correctly and safely over time.
Conclusion
The development of preservative-free multi-dose spray devices represents a significant step forward in the pharmaceutical and healthcare industries, particularly for patients who are sensitive to preservatives or have specific medical needs. Through innovations in packaging, materials science, sterilization techniques, and device design, manufacturers have overcome the challenges of microbial contamination, offering products that remain safe, effective, and preservative-free. As technology continues to evolve, we can expect even more advanced solutions that provide greater patient safety, improved convenience, and higher levels of therapeutic efficacy without the need for preservatives. This trend is not only reshaping how we think about drug delivery but also enhancing patient outcomes, particularly in chronic treatments and sensitive applications.