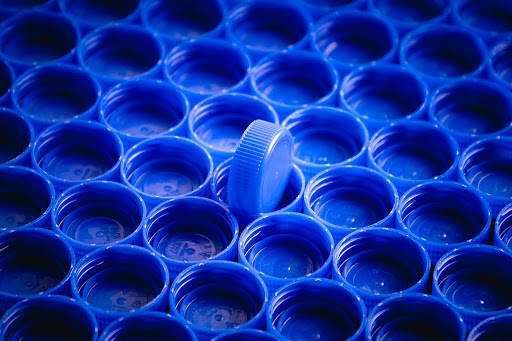
In today’s increasingly automated recycling landscape, operational efficiency and uptime are more critical than ever. Recycling facilities rely on an intricate system of machinery to process, compress, and prepare waste materials for reuse. When even a single component fails, it can cause disruptions that ripple through the entire operation. Amid the complex web of gears and hydraulic systems, one piece of equipment—often underappreciated in its importance—is the baler.
Balers are the workhorses of recycling centers, used to compress items like cardboard, plastics, and metals into compact, manageable bales. These machines help reduce volume, improve storage, and streamline transportation. But like any mechanical device under heavy use, balers are prone to wear and tear. That’s where timely and efficient service such as baler repair becomes not just a convenience but a necessity.
The role of balers in modern recycling
Balers are designed to operate continuously in high-stress environments. Depending on the material being processed, a baler may need to exert massive pressure to compress contents into dense, uniform bales. This repeated mechanical stress inevitably leads to component fatigue—hydraulic leaks, electrical faults, or even damage to structural elements like rams and chambers.
When a baler breaks down, the entire recycling process can come to a halt. Storage areas begin to overflow, materials start piling up, and deadlines become harder to meet. In a fast-paced industry driven by volumes and tight margins, downtime translates directly to lost revenue. Recycling plants are therefore increasingly investing in preventive maintenance and rapid-response repair services to stay online and operational.
On-site repair: a logistical breakthrough
One of the more transformative developments in industrial equipment servicing has been the growing prevalence of on-site repair. Rather than disassembling machinery and shipping it off for maintenance—an expensive and time-consuming endeavor—skilled technicians now travel directly to facilities with specialized tools and parts in tow.
This shift is particularly valuable for large-scale balers, which can be cumbersome to move and reinstall. On-site solutions offer several key advantages:
- Reduced downtime: Repairs can be initiated quickly, often the same day a fault is identified.
- Cost savings: Eliminating the need to transport equipment significantly reduces logistical expenses.
- Tailored service: Technicians can evaluate the machine in its actual working environment, leading to more accurate diagnostics and efficient fixes.
As recycling organizations strive for leaner operations, on-site repair services are becoming a cornerstone of their operational strategy.
A case for proactive maintenance
Though reactive repairs remain essential, forward-thinking companies are also adopting proactive maintenance protocols to extend the lifespan of their equipment. This approach involves regular inspections, timely part replacements, and performance monitoring. The goal isn’t just to fix problems when they arise, but to anticipate them before they cause disruptions.
For example, facility managers might schedule quarterly assessments of all baling equipment, check pressure levels, lubricate moving parts, and replace worn-out seals. By tracking performance data, they can identify patterns that indicate potential future failures. A sudden drop in compression efficiency, for example, may reveal a failing hydraulic pump, prompting preemptive measures.
Such maintenance routines not only reduce the frequency of breakdowns but also improve worker safety and energy efficiency. Well-maintained machines run more smoothly, use less power, and present fewer hazards to operators.
Training and workforce development
Another often-overlooked aspect of sustainable equipment management is staff training. Even the most advanced repair services can’t offset the damage caused by improper use or oversight. Recycling plants are investing in comprehensive training programs to ensure operators understand both how to use equipment correctly and how to recognize early signs of malfunction.
These programs often include modules on basic mechanical troubleshooting, understanding warning signals, and knowing when to call in professional service. Empowering workers with this knowledge creates a first line of defense against costly downtime.
Moreover, internal maintenance teams are increasingly being trained to handle minor repairs and preventive tasks, allowing outside specialists to focus on more complex issues. This hybrid approach enhances facility autonomy while still leveraging expert support when needed.
Looking ahead
As we move toward a future where sustainability and efficiency are paramount, the maintenance of recycling machinery will play a critical role in determining operational success. Services like baler repair—especially those offering on-site solutions—are no longer ancillary amenities; they are essential components of business continuity.
With increasing pressure on recycling plants to deliver faster, cleaner, and more cost-effective processes, the emphasis on equipment reliability will only grow. Facilities that prioritize proactive care, invest in workforce training, and adopt agile repair models will be better positioned to thrive in this evolving landscape.
Ultimately, in an industry built on transformation—turning waste into resource—the ability to maintain and adapt machinery ensures that nothing goes to waste, not even downtime.
Stay in touch to get more updates & news on Buzz Feed!