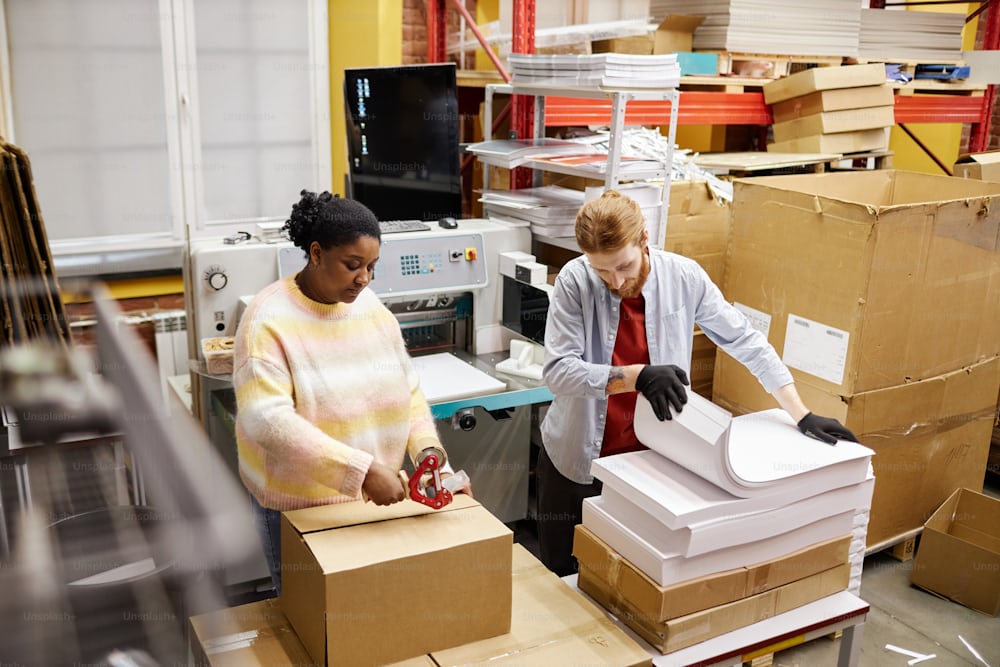
Managing work orders efficiently is critical for any business that relies on maintenance, repairs, or service operations. Traditional work order management systems often rely on manual data entry, spreadsheets, or outdated software, leading to delays, miscommunication, and errors. When work orders are not correctly assigned or tracked, businesses face increased downtime, wasted resources, and frustrated teams. The need for a smarter, more automated approach has never been greater.
Artificial Intelligence (AI) transforms work order management by introducing automation, predictive analytics, and intelligent decision-making. AI-powered systems streamline task assignments, predict equipment failures, and optimize workforce productivity. Businesses leveraging Maintainly work order solutions experience faster response times, improved accuracy, and reduced operational costs.
The Ways AI is Enhancing Work Order Management
AI brings automation, predictive insights, and real-time decision-making to work order management, making processes smoother and more efficient. These advancements reduce human error, increase productivity, and improve business operations. Here’s how AI is reshaping work order management and driving efficiency:
- Automated Work Order Creation and Assignment – Manual work order creation can be time-consuming and prone to errors. AI-powered systems analyze equipment performance, sensor data, and historical trends to generate work orders automatically. These systems assign tasks based on technician availability, skill set, and priority level, ensuring that the right personnel address issues quickly and efficiently.
- Predictive Maintenance for Reduced Downtime – Instead of reacting to breakdowns, AI enables predictive maintenance by analyzing real-time equipment data. AI algorithms detect early warning signs of equipment failures, triggering work orders before a breakdown occurs. This proactive approach minimizes downtime and extends the lifespan of assets.
- Intelligent Scheduling and Resource Optimization – AI optimizes scheduling by analyzing workforce availability, location data, and job priority levels. By considering travel time, technician workload, and urgency, AI ensures that work orders are assigned efficiently, reducing delays and maximizing productivity.
- Enhanced Communication and Collaboration – AI-powered chatbots and virtual assistants improve communication by providing instant updates, answering technician queries, and offering step-by-step troubleshooting guidance. This reduces reliance on phone calls and emails, allowing teams to focus on completing tasks.
- Data-Driven Decision Making – AI collects and analyzes vast work order data, identifying patterns and inefficiencies. Businesses can use these insights to refine processes, allocate resources more effectively, and make data-backed decisions that improve overall maintenance operations.
- Automated Inventory and Parts Management – Work order delays often occur due to missing spare parts. AI-driven systems track inventory levels, predict when parts will be needed, and trigger automatic reordering. This ensures necessary materials are available when work orders are generated, preventing disruptions.
- Improved Compliance and Reporting – Meeting compliance standards requires accurate record-keeping and timely maintenance tasks. AI automates compliance tracking, generates detailed reports, and ensures that inspections and safety procedures are completed on time, reducing regulatory risks.
The Future Of AI-Driven Work Order Management
AI is revolutionizing work order management by making operations faster, smarter, and more proactive. Businesses that integrate AI-powered maintenance software solutions gain a competitive edge through better resource utilization.
As AI evolves, work order management will become even more predictive, adaptive, and autonomous, paving the way for a future where maintenance operations are seamless and fully optimized.